Interview
Meet Juan Fernando Hidalgo Cordero, a researcher devoting his energies to unlocking the potential of the totora plant
The totora plant is a reed similar to the reedmace (aka bulrush) and grows in the Americas from California to Tierra del Fuego. Juan Fernando Hidalgo Cordero is an Ecuadorian architect, designer and researcher who has devoted considerable energies toward utilising this plant in contemporary architecture and design. “The totora plant could revolutionise sustainable production,” he argues.
-
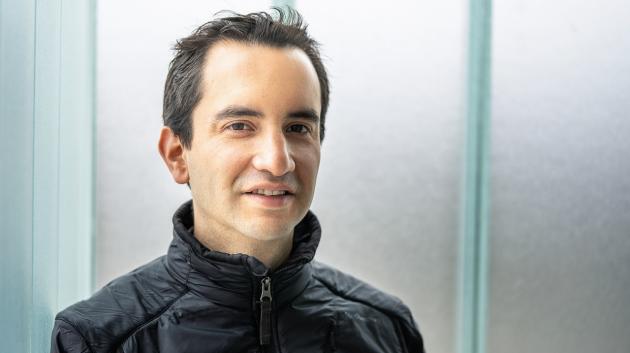
Meet Juan Fernando Hidalgo Cordero, a researcher devoting his energies to unlocking the potential of the totora plant
Meet Juan Fernando Hidalgo Cordero, a researcher devoting his energies to unlocking the potential of the totora plant
Interview by: Kateřina Přidalová; Photos from the Czech University of Life Sciences, Prague: Tomáš Rubín; Photo of Totora Textilie: Veronika Nehasilová; Translated by Dominik Jůn
► Czech version was published in Material Times Magazine 4/2019
Hidalgo is developing and expanding traditional techniques for processing the totora plant. Careful research, laboratory testing, and collaboration with local handicrafts communities is generating innovative new techniques for adapting and utilising this plant. The totora plant can be used to create both pliable and solid materials – meaning it can be used for everything from slippers to housing construction. Kateřina Přidalová met with Hidalgo in Prague; the Ecuadorian researcher had already spent time in the Czech Republic the previous year researching the totora during a stint at the Czech University of Life Sciences, Prague (ČZU).
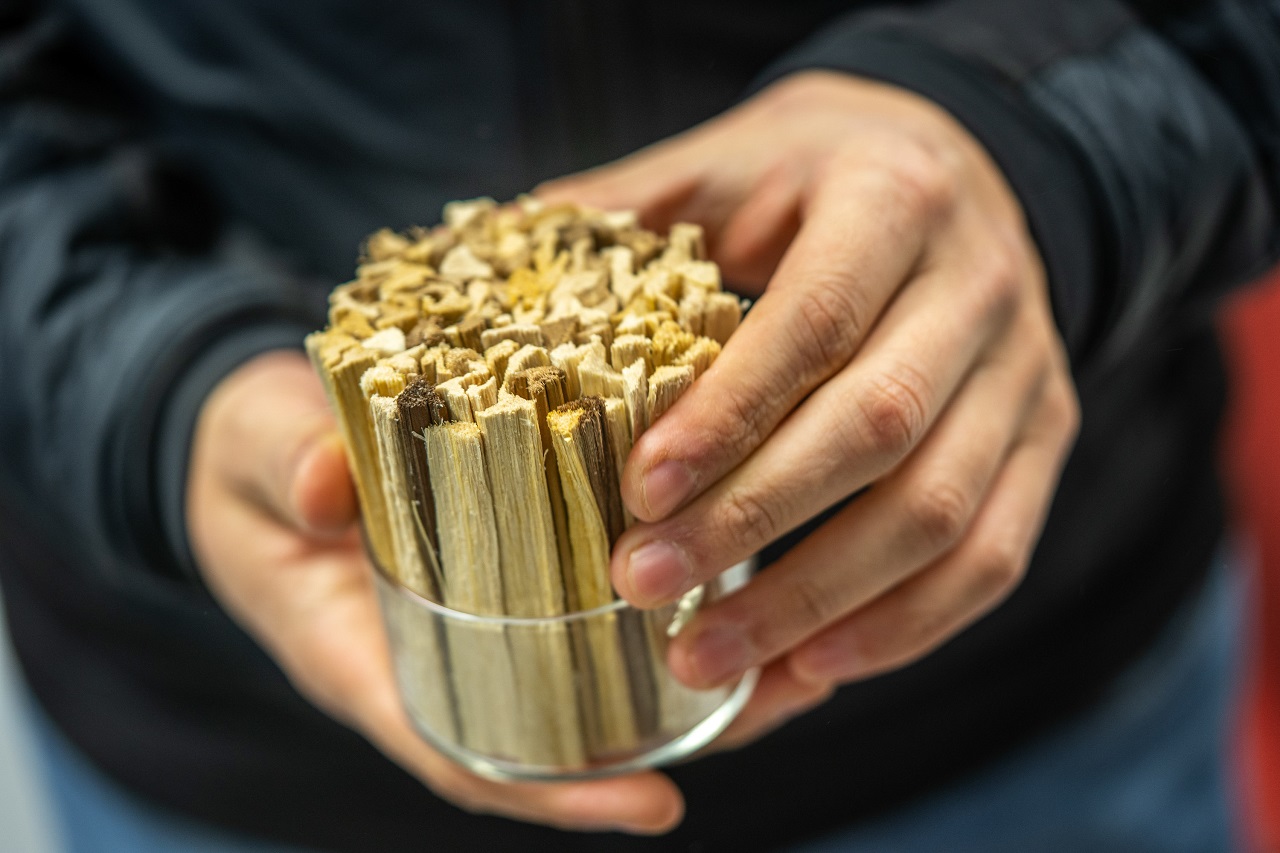
How did you end up in Prague?
My studies are based at the Polytechnic University of Madrid, where I am seeking to create a new industrial material from the totora plant. My teachers in Madrid have existing contacts with their counterparts in Prague – and because the ČZU is very well equipped with the necessary technology, they suggested I undertake a research internship here as part of my studies.
What exactly are you researching?
Presently, I am focused on the possibility of utilising the totora as an alternative to flakeboards (or OSB – compressed wood boards) used in construction. The aim is to avoid the kinds of toxic binding materials that are used in OSB production. Instead, I want to use the sugars and other compounds found in the totora itself as binding agents – because when this plant is subjected to both heat and pressure, then it releases sugars. And the resulting material also has a sweet smell.
How far along are you with this flakeboard production?
About three years ago I started researching the possibility of producing totora binderless boards. The research is still in its initial stages, and much work remains to be done. But the results so far appear promising.
So the aim is an entirely natural material that can be used in construction or furniture production. What is the wider intention that motivates such work?
In a global sense, my main aim is to spur the industrial usage of this fast-growing plant. We need to reduce the pressure on forests and the soil being caused by a growing demand for timber. Nearly 30 percent of total available land area is covered by forests (4 billion ha of 15 billion ha) and almost half of that is used for wood production (2 billion ha). Intensive logging activities, and a preference for planting fast-growing tree species, exert pressures on the land and climate. Even if the wood production cycle is more environmentally sound compared to other materials because trees are able to store CO2, and well-managed forests are a renewable material source, further considerations must nonetheless be taken into account to optimise the use of available resources and to achieve a smart model of development.
Additionally, pristine forests areas continue to be lost to mismanagement, urban development, extraction industries and agriculture. We need to realise that land is actually a limited resource that is needed to grow food, build cities, provide materials, etc. for a growing human population. Given this, studying non-wood forest products such as agricultural waste or plants with fast-growth rates such as the totora represents a chance to diversify material sources and to help reduce the pressure on conventional forests.
What makes the totora a more environmentally friendly alternative to traditional wood?
The totora grows in water – in lakes and marshes. Which means that cultivation of this plant does not place a burden on the soil. It is resistant against water level changes. And it prevents erosion. It also grows relatively fast – approximately three times faster than conifer trees. It has a natural lifecycle of one year, and so if we mow it during harvesting this actually helps to support fresh growth of the plant.
Additionally, studies have shown that totora can capture up to 73 tonnes of CO2 per ha in a managed wetland. The totora also has the potential to absorb water contaminants and improve water quality. The plant has been studied in water treatment plants in the US and South America by scientists hoping to improve the efficiency of conventional water treatment plants, or to remove nutrients from agricultural waste water via the totora’s depuration capabilities.
In addition to that, I also want to demonstrate the economic potential of utilising this plant in new ways to the traditional communities who already work with the totora. This plant has been utilised for centuries across South America for a multitude of purposes, including for the production of carpets, matting, boats, small buildings and floating islands. In fact, this plant’s use has actually been declining in recent times. Poor sales have meant that villagers, who traditionally harvested and worked the plant, have instead been migrating into urban areas in search of work.
Are the handicrafts associated with all this at risk?
Yes, there is a very real risk of losing such know-how. The harvesting and processing of the totora is becoming less economically viable. And so if we are able to demonstrate a wider range of uses for the plant, then this could help to preserve such handicraft traditions. Local producer communities know very well how to harvest, cut and process the plant. All we want to do is to demonstrate additional opportunities for selling end products, which could further encourage the conservation of totora habitats and their associated ecosystems.
The somewhat similar reedmace grows throughout the Czech Republic, and was once used for weaving baskets or hats. Has your research also focused on this plant?
My research is mainly centred on the totora plant. Nonetheless, my research findings can also be applied to similar plants. The methods and principles may apply mutually. The reedmace is a very interesting plant. It also grows in water and marshes, and German scientists have been studying this family of plants for use in insulating materials.
The cells of the totora plant are, to a large degree, filled with air. How does that affect the properties of this material?
The plant grows to an average height of three metres, with an average width of one centimetre. It has an outer skin which is harder, while the inside pith is comprised of a airy chamber vascular bundle somewhat akin to a sponge. As a result of its airy cellular structure, the texture of this pith is soft, elastic and resilient. The air pockets within the stem are between 0.5-5mm long, and about 1mm wide. In a physiological sense, these chambers play a very important role for the plant – allowing water to permeate, as well as gases to travel from the tip to the roots, and absorbing carbon dioxide. They are highly adapted to moist conditions, and that enables the resulting material to be amenable to surface treatment. At the same time, they dry quickly, which saves energy during production.
One of the material innovations that you have already brought to the market is called “Totora Textile”. Can you tell us how this came about?
I wanted to study all of the possibilities inherent in this particular plant-based material. I examined how the plant looked internally, and discovered a very interesting texture, which has a pleasant aroma, and furthermore is warmer in cool conditions and cooler in warmer weather.
Your particular plant processing methodology is notable for the fact that you don’t cut the plants lengthways – as is the common practice – but rather perpendicularly. You then reconnect these cut stems to each other...
The difference with my methodology is that traditional processors mostly utilise stems cut lengthways. Conversely, “Totora Textiles” utilise the plant’s transversal section, exposing the internal pithy components, which contain the aforementioned sugary binding agent. Another advantage is that the sponge-like structures of the stems bind very well to primers.
Unlike the totora version of OSB flakeboards, which are rigid, this particular material is pliable. Which is also evidently due to the fact that the individual stems are able to fall into place among each other with remarkable precision...
Sometimes it can appear to be counter-intuitive – you see a material that looks like it is firm, but then you touch it and you sense that it is soft and pliable. This effect is the result of using many parts of the stem, which are locked into place via the use of a vibrating ledger, and are subsequently binded on a joist. When you press down on the finished product, it yields. I used this effect for a bench that I designed.
Asides from this bench you mentioned, your website also features many product designs, including slippers, doormats, pillows, all the way to a shapeable table. Are these just prototypes, that feature in gallery exhibitions and design trade fairs, or are they available to purchase?
Yes, those products are available to purchase. For example, three galleries across Europe actually offer the totora bench. And the tables can be ordered from Ecuador – alas, they are not yet available via any European gallery.
Do you wear totora slippers at home?
Yes, we use them back home in Ecuador. Our home is like a museum. It has doormats, slippers, totora wall dividers, and other artefacts. I first test all of my experiments at home.
How did you get the idea to create a shapeable table? It is certainly a very distinctive piece of furniture.
I was inspired by toy known as a “Pin Sculpture”. They are built with plastic or metallic pins welded in a perforated support, and when you push the pins you change the shape of the surface. I wanted to adopt the idea of such surfacing, which can be utilised both vertically as a wall or horizontally as a table. Recently, I also designed a sofa based around a similar principle. Sitting in it is a very interesting experience, because it feels as if one is swimming, engulfed in totora. It was very relaxing.
In essence, this is a form of conceptual design. I was inspired by the thought that people always somehow try to conform their surrounding environment according to their needs. I wanted to create a customisable and adaptable surface, which will be functional irrespective of whether it is serving as a table, wall or anything else. When we presented the design during the Design Week in Paris, we ended up being approached by a man working in the tourist cruiser industry. He was interested in the idea of a table that would be able to hold cups or tableware even while the boat itself was moving. Such a table can be utilised in aircraft as well – and indeed anywhere in which the environment is in motion. But one ongoing problem is that the material is highly absorbent...
So how can water-resistance be increased?
One option is to use wax – bee and paraffin-based. This will seal the surface. But this is a temporary solution, meaning that a fresh layer would have to be applied around once a year. Other options include using chemical modifications or surface varnish – those normally used to treat wood. These are certainly far more durable than wax. We haven’t tested these yet, but this should work.
Are your totora products intended only for interior use, or could, under certain conditions, they also be used outdoors?
Right now, they are only for use in interiors, but should more research be applied into the field of increasing water-resistance, then such products will also be usable outdoors. After all, boats made from totora using traditional techniques are able to endure a more than three-month-long trip in the high seas. [Readers can monitor the progress of the Viracocha 3 reed raft expedition that sailed from Chile to Australia this March.] And so the plant does possess a degree of its own water-resistance; but more research needs to be done into increasing that.
When and how did you begin to take an interest in natural materials and handicraft adaptations? Did you learn directly from traditional communities in Ecuador?
When I was studying architecture, I came across man-made floating islands in Lake Titicaca. In purely architectural design terms, they helped to create a fascinating addition to the landscape. And all of these were made from totora. After that I began to study local Ecuadorian communities and to learn the techniques and principles of working materials. There are traditional steps, for example in the weaving of doormats, in which a moistened material is used, which is weighed down with stones in order to flatten it. And then my acquaintance with these traditional methods helped me to turn my attention towards designing new products. But at the outset, one needs to have a healthy respect for the people involved in production and the materials that they use.
I recently interviewed (Czech artist and research designer) Petra Gupta Valentová. Working in conjunction with local fabric printers in India, Valentová creates new fabric designs utilising traditional woodblock printing techniques. During my interview, Valentová mentioned “co-design” principles, in which the design and manufacturing process is a collaborative effort – meaning that notions of merely monetising labour skills through the creation of handicraft products to be sold in Western stores are negated. How close are your contacts with the traditional communities associated with your craft?
My workshops include members of a family that works with the totora plant. When I need to purchase more totora then I go to them, because I know that they will always pre-select and prepare the kind of material that I require. Sadly, they are one of just a handful of seller-suppliers of this plant.
So you only purchase material from them? You don’t consult them over design questions related to your products?
No, they do not possess the expertise that I have developed in that field. They merely help me, and offer guidance on traditional uses for the totora plant. We don’t work together on designs, but rather on questions such as how the material acts when it is cut. We both learn from each other. This community is based in the town of Cuenca, where I also live. The city of Otavalo also contains another, better organised handicraft group, which works with designers on developing projects. Among the matters tackled there are issues such as the latest weaving techniques that combine nylon or metallic materials.
You must also consider your research from a business point of view – do you plan to set up your own brand in the future?
The materials and techniques associated with totora textile production are protected not by commercial trademarks, but by the kind of copyright protections that apply to creative works. Such protections serve as a good guarantee to ensure quality.
At present, your totora textiles are made by hand. Are you also considering industrial scale production?
If demand grows, then industrial manufacturing of this material could also be considered. Nonetheless, many of the products associated with the totora plant are made by hand partly to preserve traditional manufacturing processes, and to support handicraft labour.
But that is surely not the case with a product such as flakeboards, which could serve as an alternative to existing OSBs. In this case, is industrial demand and manufacturing a promising avenue of opportunity to expand production?
Yes, in the case of totora boards there is already a market for similar products such as OSB or MDF boards. So totora binderless boards may have the advantage of being made without using chemical glues, which might be an important improvement over the existing options without compromising other characteristics. Due to the fast-growth rate of the plant it could be possible to achieve a constant supply of material from a relatively small planting area, and the material production cycle can be paired with other services such as the water cleaning facilities of marshland restoration projects. These kinds of commercial advantages could make totora boards more competitive on an industrial production level.
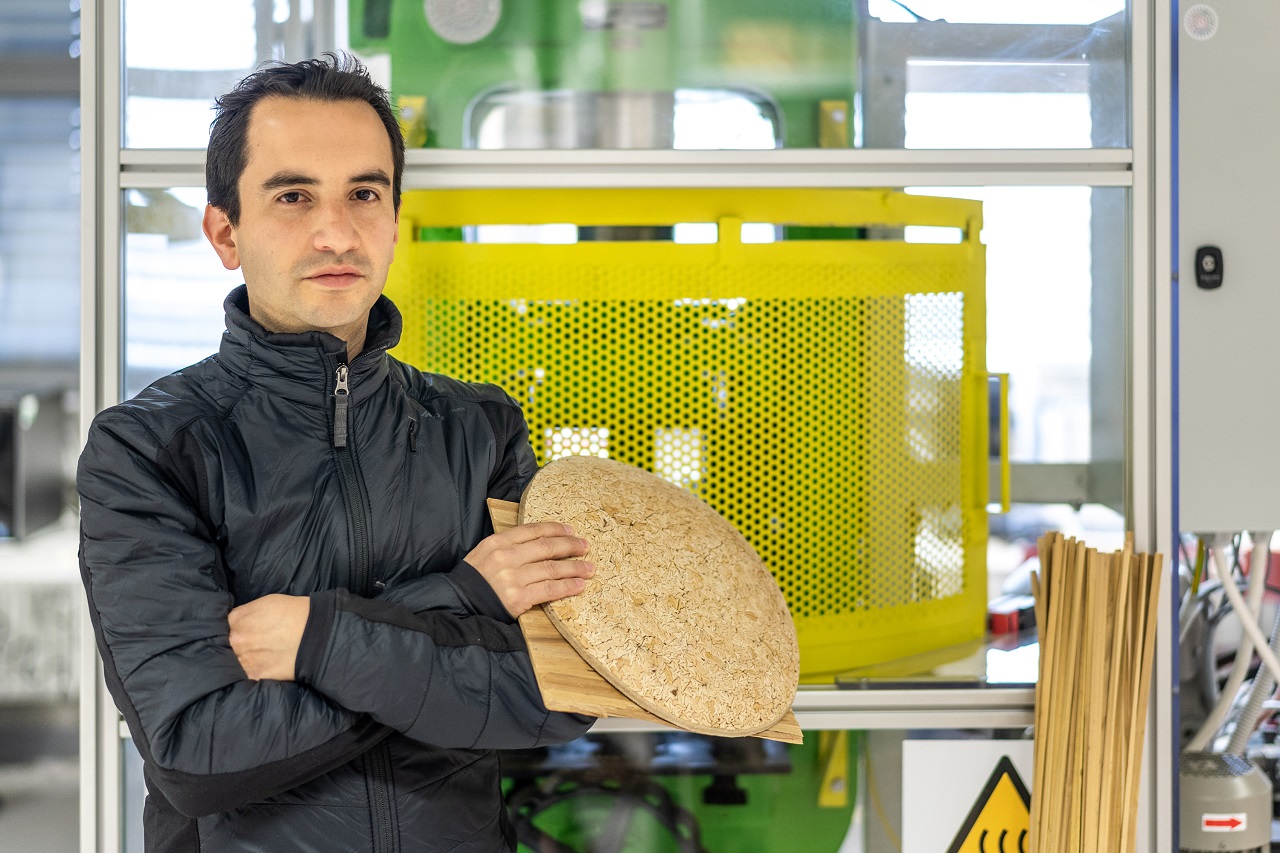
During a recent lecture at the Academy of Arts, Architecture and Design in Prague (UMPRUM), you mentioned that one of the reasons the European market hitherto lacks demand for totora is that it remains an unknown material for most consumers. What would have to happen to improve such perceptions in Europe?
If you have publicity, then you can sell almost anything. And if you also successfully demonstrate the environmental and socio-economic benefits of the production and utilisation of the totora, then you stand a chance of real success. We conducted some important steps in this regard as far back as 2014, when I obtained UNESCO recognition for the totora project, which positively appraised the handicraft traditions, innovation, and social aspects associated with the totora plant.
You also said that the biggest factor impacting the end cost of totora products is the need to import this material from Ecuador. Which is ultimately not a very environmentally friendly approach. Would it not instead be more commercially viable to utilise your existing knowledge to process similar local materials such as the aforementioned reedmace?
Yes, that could indeed be a better and more environmentally-sound solution. But the question remains as to whether anyone exists here who is devoted to harvesting reedmace, and whether there are people here who know how to properly work with this plant. Certainly that needs to be further investigated. But in essence, my work with the totora plant is centred around conceptual design, developed in conjunction with a specific traditional community, and with a specific aim of expansion into other markets. The traditions associated with this inherently represent part of the material’s value, and this also adds to the commercial viability of seeking foreign export markets. I want to demonstrate that however traditional this material is, it still also offers modern application possibilities in contemporary design. These principles could certainly be replicated for other interesting materials such as the reedmace, with studies undertaken of their own associated traditions and applications.
The idea is for awareness of the totora to grow, and for people to seek it out as a beautiful, quality and multifunctional material. But my main intention with regards to the pieces I have designed is not to establish a volume-oriented production model, but rather to create more beautiful products from the totora that further highlight the material’s beauty and characteristics; and through this to celebrate the history, culture and traditions behind the totora plant, which I believe are a crucial part of our global heritage.

27. 6. 2019